This firm originally adopted a jet-tube air sparger in 150m3 amino acid fermentors (Fig.2)
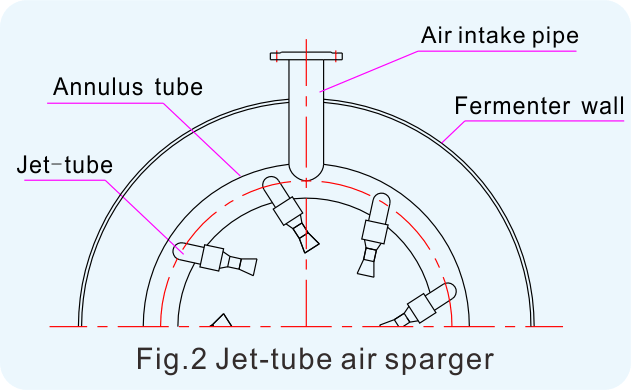
Existing problem
From practical observations, jet-tube air sparger required high pressure head as driving force. It added load of air compressors, and due to pipeline resistance in real production, flow velocity in the jet tube cannot achieve design value, impacting gas dispersion effect.
In view of maintenance, jet tube had a complex structure with excessive connectors, causing broth scaling and sterilization failure. To ensure safe production, it had to unload every single jet tube for cleaning, increasing maintenance workload and was prone to contamination.
Moreover, jet-tube has a high velocity with strong shear force, so it will cause mechanical damage to certain filamentous microorganisms such as mould and some bacillus, disrupt normal cell growth, and extend batch cycle.
Implementation of fermentor modification
Vortex G-L mixer serves as a layer of stirrer, so the original stirrer configuration can be optimized. Draft tube was retained, jet-tube sparger was removed, installed vortex G-L mixer at the bottom, replaced the upper 6-leaf parabola turbine with a 4-leaf impeller. The flow pattern changed from upward to downward in the draft tube, axial flow motion was strengthened with adequate radial gas dispersion. As shown in Fig.3.
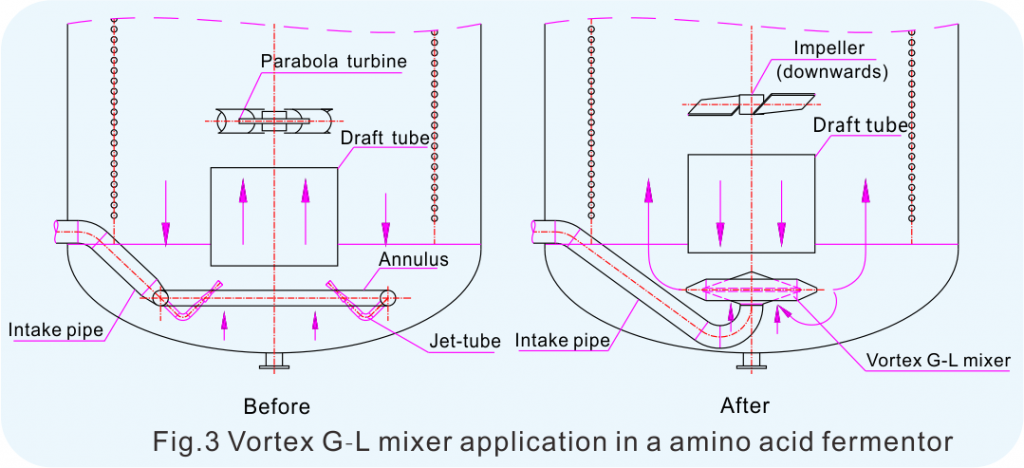
Fermenter modification results:
Indicators changed as shown in Table. 1
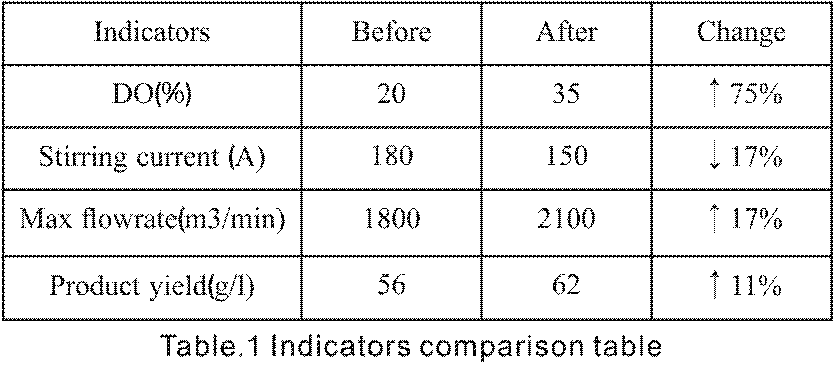
Conclusions based on practical evaluations:
(1) DO improved dramatically.
(2) Stirrer shaft current dropped remarkably.
(3) Max air flow rate increased, wider regulation range.
(4) Product yield increased.
(5) Better broth mixing, stable liquid level.